Copper Finned Grooved Tube

Surface of the copper pipe has a certain number of metal ribs with a certain helix angle. Compare to plain copper tube, grooved copper tube has a 20%-30% improvement of heat radiation performance. The internal grooved structure of the copper pipe improves the laminar flow state in the pipeline system, the cycle is stable and efficient, the heat exchange efficiency is greatly improved, and the operating cost is reduced.
As a high-efficiency heat transfer element, the internally threaded copper tube is widely used in the condenser and evaporator of the air-conditioning system with high-efficiency aluminum or aluminum alloy fins.
The energy-saving, high-efficiency and miniaturization requirements of air-conditioning systems have greatly promoted the improvement of compressor performance, and increased the use of high-efficiency and miniaturized condensers and evaporators.
Since the 1980s, people began to use internally threaded copper tubes. With the continuous improvement and progress of internally threaded forming technology, internally threaded copper tubes have developed in the direction of thin wall, high teeth, light weight, small diameter, and high-efficiency heat transfer.
Enhanced evaporation tube
Enhanced evaporator tubes are mainly used in centrifugal refrigerators, water chillers and shell-and-tube heat exchangers with small temperature differences.
The enhanced evaporation tube is a new type of heat exchange tube that can generate strong vaporization and boiling on the outer surface. Its excellent heat conduction ability comes from a unique microporous structure, and this optimized microporous structure is not just a simple.
The heat exchange area is enhanced, and a large number of vaporization cores required for evaporative heat exchange are increased, which changes the evaporation flow mode of the refrigerant and helps to remove impurities and reduce fouling, reduces the external thermal resistance of the tube, and significantly improves the external heat transfer efficiency; the inner surface of the tube is also processed with spiral grooves to further increase the heat transfer area and turbulence of the inner surface and reduce the thermal resistance inside the tube.
The enhanced heat transfer efficiency inside and outside the tube of the enhanced evaporator tube has greatly promoted the comprehensive heat transfer capacity of the tube type, and the volume and weight of the heat exchanger can also be reduced accordingly to meet the requirements of energy saving and cost reduction.
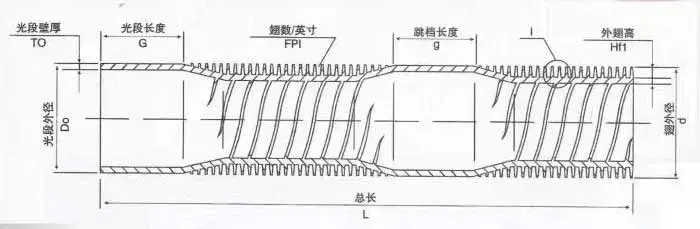
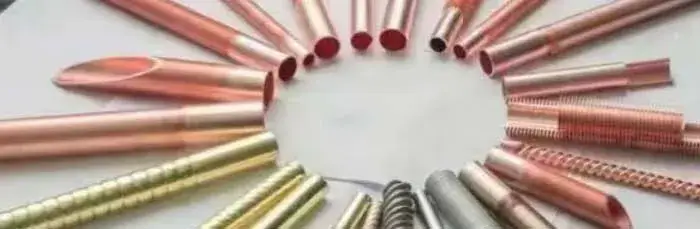
Manufacturing Standard | GB/T19447 or equivalent standard ASTM B359, ASME SB359 | |
---|---|---|
Copper Alloy | Cu-DHP, C12200, TP2, C1220 | |
Temper Condition | Option 1: Finned part half hard, plain part annealed | Option 2: Annealed temper for entire tube |
Packing | Wooden Case | |
Dimensions Range | ||
Do | 15.88-25.4mm | |
To | 1.0-1.5mm | |
HPI | ≤0.70mm | |
FPI | 40-56 teeth | |
Overall Length | ≤11 meters |