ASTM B188 Seamless Copper Bus Pipe and Tube for Electrical Conductors
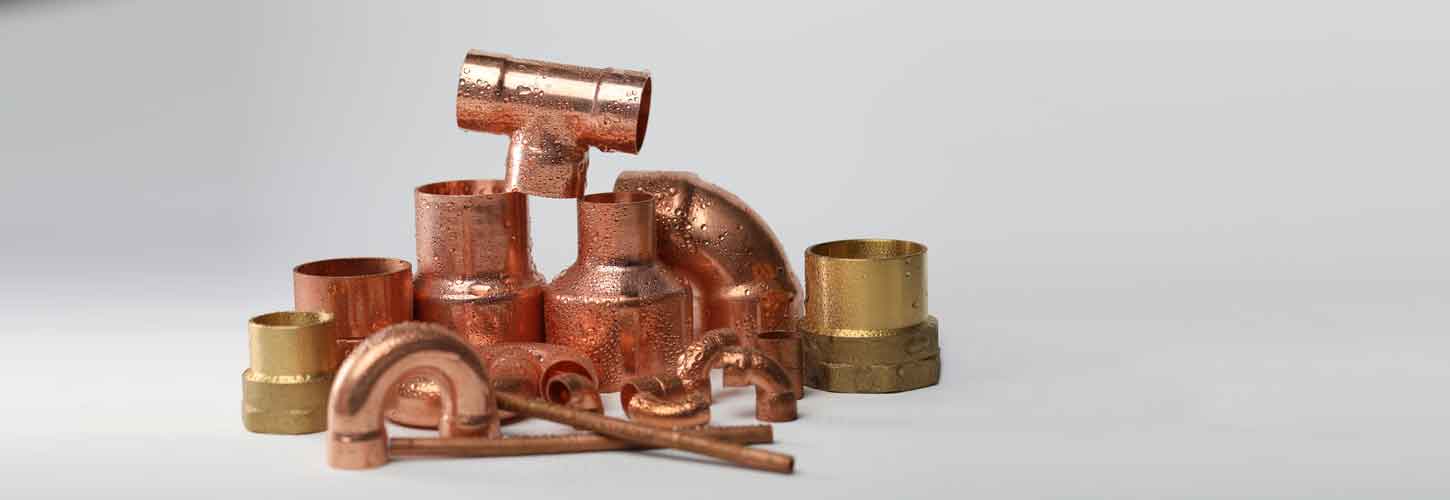
ASTM B188 Seamless Copper Bus Pipe and Tube for Electrical Conductors
1. Scope
1.1 This specification establishes the requirements for seamless copper bus pipe and tube intended for use as electrical conductors.
1.1.1 The product shall be made from one of the following coppers, as denoted in the ordering information:
Copper UNS No. | Previously Used Designation | Type of Copper |
---|---|---|
C10100 | OFE | Oxygen-free, electronic |
C10200 | OF | Oxygen-free, without residual deoxidants |
C10300 | - | Oxygen-free, extra low phosphorus |
C10400, C10500, C10700 | OFS | Oxygen-free, silver bearing |
C11000 | ETP | Electrolytic tough pitch |
C11300, C11400, C11600 | STP | Silver-bearing tough pitch |
C12000 | DLP | Phosphorized, low residual phosphorus |
1.2 Unless otherwise specified, any one of the above coppers may be furnished.
1.3 The values stated in inch-pound units are the standard. The SI values given in parentheses are for information only.
2. Referenced Documents
2.1 ASTM Standards:
B 193 Test Method for resistivity of Electrical Conductor Materials
B 428 Test Method for Angle of Twist in Rectangular and Square Copper and Copper Alloy Tube
B 577 Test Methods for Detection of Cuprous Oxide (Hydrogen Embrittlement Susceptibility) in Copper
B 601 Classification for Temper Designations for Copper and Copper Alloys -- Wrought and Cast
B 846 Terminology of Copper and Copper Alloys
E 8 Test Methods for Tension Testing of Metallic Materials
E 18 Test Methods for Rock well Hardness and Rockwell Superficial Hardness of Metallic Materials
E 29 Practice for Using Significant Digits in Test Data to Determine Conformance with Speicifications
E 53 Test Methods for Determination of Copper in Unalloyed Copper by Gravimetry
E 62 Test Methods for Chemical Analysis of Copper and Copper Alloys (Photometric Methods)
E 243 Practice for Electromagnetic (Eddy-Current) Examination of Copper and Copper-Alloys Tubes
E 255 Practice for Sampling Copper and Copper Alloys for Determination of Chemical Composition
E 527 Practice for Numbering Metals and Alloys
3. Terminology
3.1 For definitions of terms related to copper and copper alloys, refer to Terminology B 846
3.2 Definitions:
3.2.1 bus pipe or tube -- a high conductivity copper tubular product used as an electrical conductor.
4. Ordering Information
4.1 Include the following information when placing orders for product under this specification:
4.1.1 ASTM designation and year of issue.
4.1.2 Copper UNS designation.
4.1.3 Temper (Section 7),
4.1.4 Dimensions and form ( Section 14),
4.1.5 Length (Section 14)
4.1.6 Total Quantity of each size (Table 1)
4.1.7 Quantity of each item,
4.2 The following options are available under this specification and should be specified in the contract or purchase order when required:
4.2.1 Bend test (Section 10)
4.2.2 Hydrogen embrittlement susceptibility test (Section 12)
Nominal or Standard Pipe Size, in. | Dimensions, in. (mm) | Cross-Sectional Area of Wall, in. (mm) | Theoretical Weight, lb/ft (kg/m) | ||
---|---|---|---|---|---|
Outside Diameter | Inside Diameter | Wall Thickness | |||
Regular | |||||
1/4 | 0.540(13.7) | 0.376(9.55) | 0.082(2.08) | 0.118(0.761) | 0.457(0.680) |
3/8 | 0.675(17.1) | 0.495(12.6) | 0.090(2.29) | 0.165(1.06) | 0.641(0.954) |
1/2 | 0.840(21.3)) | 0.626(15.9) | 0.107(2.72) | 0.246(1.59) | 0.955(1.42) |
3/4 | 1.050(26.7) | 0.822(20.9) | 0.114(2.90) | 0.335(2.16) | 1.30(1.93) |
1 | 1.315(33.4) | 1.063(27.0) | 0.126(3.2) | 0.471(3.04) | 1.82(2.71) |
1-1/4 | 1.660(42.2) | 1.368(34.7) | 0.146(3.71) | 0.694(4.48) | 2.69(4.00) |
1-1/2 | 1.900(48.3) | 1.600(40.6) | 0.150(3.81) | 0.825(5.32) | 3.20(4.76) |
2 | 2.375(60.3) | 2.063(52.4) | 0.156(3.96) | 1.09(7.03) | 4.22(6.28) |
2-1/2 | 2.875(73.0) | 2.501(63.5) | 0.187(4.75) | 1.58(10.2) | 6.12(9.11) |
3 | 3.500(88.9) | 3.062(77.8) | 0.219(5.56) | 2.26(14.6) | 8.75(13.0) |
3-1/2 | 4.000(102) | 3.500(88.9) | 0.250(6.35) | 2.95(19.0)) | 11.4(17.0) |
4 | 4.500(114) | 4.000(102) | 0.250(6.35) | 3.34(21.5) | 12.9(19.2) |
5 | 5.562(141) | 5.062(129) | 0.250(6.35) | 4.17(26.9) | 16.2(24.1) |
6 | 6.625(168) | 6.125(156) | 0.250(6.35) | 5.01(32.3) | 19.4(28.9) |
8 | 8.625(219) | 8.001(203) | 0.312(7.92) | 8.15(52.6) | 31.6(47.0) |
10 | 10.750(273) | 10.020(255) | 0.365(9.27) | 11.9(76.8) | 46.2(68.7) |
12 | 12.750(324) | 12.000(305) | 0.375(9.52) | 14.6(94.2) | 56.5(84.1) |
Extra Strong | |||||
1/4 | 0.540 (13.7) | 0.294 (7.47) | 0.123(3.12) | 0.161(1.04) | 0.625(0.930) |
3/8 | 0.675(17.1) | 0.421(10.7) | 0.127(3.23) | 0.219(1.41) | 0.847(1.26) |
1/2 | 0.840(21.3) | 0.542(13.8) | 0.149(3.78) | 0.323(2.08) | 1.25(1.86) |
3/4 | 1.050(26.7) | 0.736(18.7) | 0.157(3.99) | 0.440(2.84) | 1.71(2.54) |
1 | 1.315(33.4) | 0.951(24.2) | 0.182(4.62) | 0.648(4.18) | 2.51(3.73) |
1-1/4 | 1.660(42.2) | 1.272(32.3) | 0.194(4.93) | 0.893(5.76) | 3.46(5.15) |
1-1/2 | 1.900(48.3) | 1.494(37.9) | 0.203(5.16) | 1.08(6.97) | 4.19(6.232) |
2 | 2.375(60.3) | 1.933(49.1) | 0.221(5.61) | 1.50(9.68) | 5.80(8.63) |
2-1/2 | 2.875(73.0) | 2.315(58.8) | 0.280(7.11) | 2.28(14.7) | 8.85(13.2) |
3 | 3.500(88.9) | 2.892(73.6) | 0.304(7.72) | 3.05(19.7) | 11.8(17.6) |
3-1/2 | 4.000(102) | 3.358(85.3) | 0.321(8.15) | 3.17(23.9) | 14.4(21.4) |
4 | 4.500(114) | 3.818(97.0) | 0.341(8.66) | 4.46(28.8) | 17.3(25.7) |
5 | 5.562(141) | 4.812(122) | 0.375(9.52) | 6.11(39.4) | 23.7(35.3) |
6 | 6.625(168) | 5.751(146) | 0.437(11.1) | 8.50(54.8) | 32.9(49.0) |
8 | 8.625(219) | 7.625(194) | 0.500(12.7) | 12.8(82.6) | 49.5(73.7) |
10 | 10.750(273) | 9.750(248) | 0.500(12.7) | 16.1(104) | 62.4(92.9) |
4.2.3 Microscopical examination (Section 11)
4.2.4 Temsion testing (Section 9)
4.2.5 Eddy-current test (Section 13)
4.2.6 Certification (Section 23)
4.2.7 Mill test report (Section 24), and
4.2.8 Special packaging, if required (Section 25)
5. Materials and Manufacture
5.1 Material:
5.1.1 The material of manufacture shall be case billet of one of the UNS copper alloy numbers included in the scope, and as so specified in the contract or purchase order, and shall be of such soundness as to be suitable for processing into lengths of pipe or tube for the intended application.
5.2 Mannufacture:
5.2.1 The material shall be manufactured by such hot-working, cold-working , and annealing processing as to produce a uniform, seamless wrought structure in the finished product.
5.2.2 The method of manufacture shall be such that the finished material conforms to the specified temper properties ( see7.1).
6. Chemical Composition
6.1 The material shall conform to the requirements in Table 2 for the copper UNS No. specified in the ordering information.
6.2 These composition limits do not preclude the presence of other elements. Limits for unnamed elements may be established and analysis required by agreement between the manufacturer or supplier and purchase.
7. Temper
7.1 The material shall be furnished in either the O60 (soft anneal) or H80 (hard drawn) temper as defined in Classification B 601. The requirements are specified in Table 3.
8. Electrical Resistivity Requirements
8.1 The material shall conform to the maximum electrical resistivity requirements prescribed in Table 3.
9. Mechanical Property Requirements
9.1 The product shall conform to the mechanical property requirements prescribed in Table 3.
9.1.1 Tension testing for tensile and elongation information need not be performed except when indicated by the purchaser at the time of placing the order ( see 4.2.4)
9.1.2 The tension test shall be used to resolve cases of dispute.
9.2 All test specimens shall be tested in full size when practicable. When a machined specimen becomes necessary for any test required under this specification, enough metal shall be suitably removed from the sample to meet the limitations of the testing facilities.
Element | Composition, % | ||||||||||
---|---|---|---|---|---|---|---|---|---|---|---|
Copper UNS No. | |||||||||||
C10100 | C10200 | C10300 | C10400B | C10500B | C10700B | C11000 | C11300C | C11400C | C11600C | C12000 | |
Copper (incl silver), min | 99.99D | 99.95 | 99.95E | 99.95 | 99.95 | 99.95 | 99.90 | 99.90 | 99.90 | 99.90 | |
Phosphorus | A | ... | 0.001-0.005 | ... | ... | ... | ... | ... | ... | ... | 0.004-0.0012 |
Oxygen, max | 0.0005 | 0.0010 | ... | 0.0010 | 0.0010 | 0.0010 | ... | ... | ... | ... | ... |
Silver | A | ... | ... | 8F | 10F | 25F | ... | 8F | 10F | 25F | ... |
A Impurity maximums in ppm of C10100 shall be: antimony 4, arsenic 5, bismuth 1.0, cadmium 1, iron 10, lead 5, manganese 0.5, nickel 10, phosphorus 3, selenium 3, silver 25, sulfur 15, tellurium 2, tin 2, and zinc 1.
B C10400,C10500, and C10700 are oxygen-free coppers with the addition of a specified amount of silver. The compositions of these alloys are equivalent to C10200 plus the intentional addtion of silver.
C C11300, C11400, C11500, and C11600 are electrolytic tough-pitch copper with silver additions. The compositions of these alloys are equivalent to C11000 plus the intentional addition of silver.
D Copper shall be determined by difference between "impurity total" and 100%.
E Copper (includes silver) + phosphorus, min.
F Values are minimum silver in troy ounces per avirdupois ton (1 oz/ton is equivalent to 0.0034%).
10. Performance Requirements
10.1 Bend Test Requirements:
10.1.1 The product shall conform to the bend testing requirements prescribed in Table-3.
10.1.2 Bend testing need not be performed except when specified by the purchaser at the time of placing the ordrer (see 4.2.1).
10.2 Microscopical Examination:
10.2.1 The test specimens of material designated as Copper UNS Nos. C10100, C10200, C10300, C10400, C10500, C10700, and C12000 shall be free of cuprous oxide as determined by Procedure A of Test Methods B577. In case of a dispute, a referee method in accordance with Procedure C shall be used.
10.2.2 The test need not be performed except when specified at the time of placing the order (see 4.2.3).
10.3 Hydrogen Embrittlement Susceptibility Test:
10.3.1 When tested, material designated as Copper UNS Nos. C10100, C10200, C10300, C10400, C10500, C10700, and C12000 shall pass the embrittlement test of Procedure B of Test Methods B577. The actual performance of this test is not mandatory under the terms of this specification unless specified in the ordering information (see 4.2.2). In case of dispute, a referee method in accordance with Procedure C of Test Methods B577 shall be employed.
11. Other Rrequirements
11.1 Nondestructive Testing:
11.1.1 When specified (see 4.2.5), the product shall be tested in the final size but may be tested before the final anneal or heat treatment, when these thermal treaments are required, unless otherwise agreed upon by the manufacturer or supplier and purchaser.
11.1.2 Eddy-Current Test -- When specified, each piece of product from 1/8 inches (3.2-mm) up to and including 3-1/8 - inches (79.4-mm) nominal outside diameter, or 2-1/2-inches (63.5-mm) distance between outside parallel surfaces, shall be subjected to an eddy-current test. Testing shall follow the procedures of Practice E243 except for determination of "end effect." The product shall be passed through and eddy-current testing unit adjusted to provide information on the suitability of the product for the intended application.
11.1.3 Notch-depth standards rounded to the nearest 0.001 inches (0.025mm) shall be 22% of the nominal wall thickness. The notch depth tolerance shall be +/- 0.0005 inches (0.013mm). Alternatively, when the test is performed using speed-insenstitive equipment that can select a maximum imbalance signal, a maximum imbalance signal of 0.3% shall be used.
11.1.4 Product that does not actuate the signaling device of the eddy-current test shall be considered as conforming to the requirements of this test. Product with discontinuities indicated by the testing unit may be reexamined or retested, at the option of the manufacturer, to determine whether the discontinuity is cause for rejection. Signals that are found to have been caused by minor mechanical damage, soil, or moisture shall not be cause for rejection of the product provided the dimensions of the product are still within prescribed limits and the product is suitable for its intended application.
12. Dimensions, Weights, and Permissible Variations
12.1 General -For the purpose of determining conformance with the dimensional requirements given in this specification, any measured value outside the specified limiting values for any dimension may be cause for rejection.
12.2 Dimension and Weight - The dimensions and weights for nominal or standard copper pipe of various outside diameters shall be as prescribed in Table 1.
12.3 Weight Tolerances - The weight of the nominal or standard pipe shall not vary from the theoretical weight per foot prescribed in Table 1 by more than the following:
Nominal or Standard Pipe Size, in. | Weight Tolerance, % |
---|---|
6 and under | 5 |
Over 6 to 8, incl | 7 |
Over 8 | 8 |
12.4 Thickness Tolerances - The wall thickness of nominal or standard pipe at any point shall not be less than that prescribed in Table 1 by more than the following:
Nominal or Standard Pipe Size, in. | Thickness Tolerance, % |
---|---|
6 and under | 5 |
Over 6 to 8, incl | 7 |
Over 8 | 8 |
Note: Thickness tolerance in aboving table expressed to the nearest 0.001 in. (0.025 mm).
12.5 Copper Tube (Other than Pipe):
12.5.1 Round Tube - Wall thickness tolerances shall be in accordance with Table 4. Diameter tolerances shall be in accordance with Table 5.
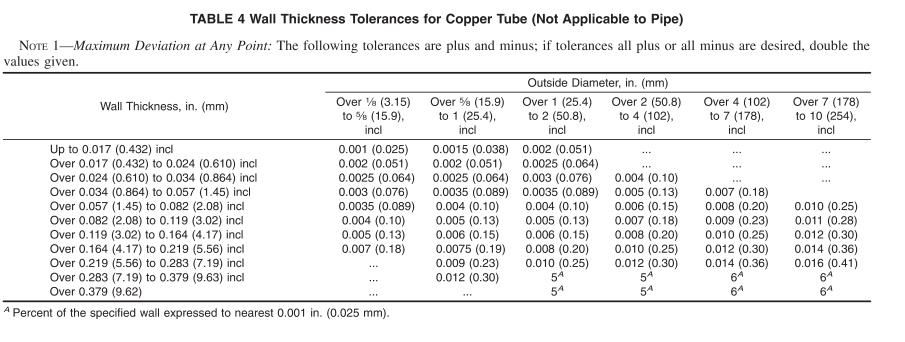
Specified Diameter, in. (mm) | Diameter to Which Tolerance Applies | Tolerance, plus and minus, in. (mm) |
---|---|---|
Up to 5/8 (15.9), incl | inside or outside | 0.002 (0.051) |
Over 5/8 (15.9) to 1 (25.4), incl | inside or outside | 0.0025 (0.64) |
Over 1 (25.4) to 2 (50.8), incl | inside or outside | 0.003 (0.076) |
Over 2 (50.8) to 3 (76.2), incl | inside or outside | 0.004 (0.10) |
Over 3 (76.2) to 4 (102), incl | inside or outside | 0.005 (0.13) |
Over 4 (102) to 5 (127), incl | inside or outside | 0.006 (0.15) |
Over 5 (127) to 6 (152), incl | inside or outside | 0.007 (0.18) |
Over 6 (152) to 8 (203), incl | inside or outside | 0.008 (0.20) |
Over 8 (203) to (254), incl | inside or outside | 0.010 (0.25) |
No result, please contact our sales team by emailing info@winlandmetal.com for more information.