Knowledges about non-ferrous metals you may not know
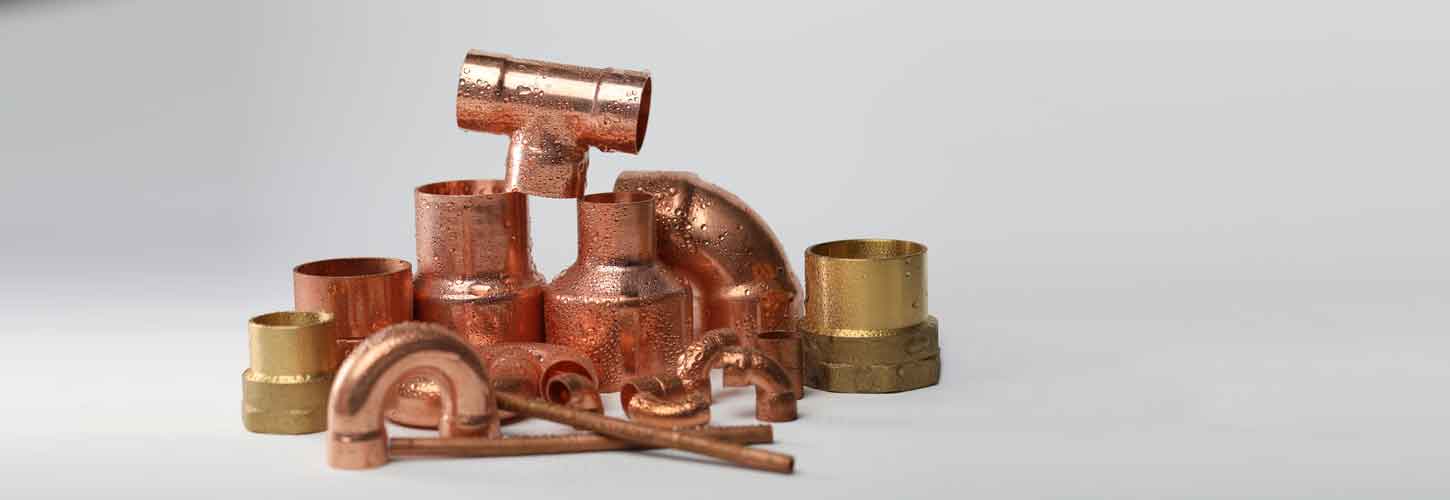
Non-ferrous metals are relative to ferrous metals. In the large family of more than 80 metals, all metals except iron, manganese and chromium are non-ferrous metals. Commonly used non-ferrous metals are copper, aluminum, lead, zinc, nickel, tin, magnesium, titanium, cadmium, antimony, cobalt, tungsten, molybdenum, vanadium, etc.
Copper and its alloys
The fresh fracture of copper is rosy, and it becomes reddish brown due to covering with a layer of oxide film. Its density is 8.9 g/cm3, melting point is 1083 ℃, boiling point is 2580 ℃, and thermal conductivity is 0.98 cal/(cm.s. ℃), the resistivity is 0.017 241Ωmm2/m, and the surface oxides include CuO and Cu2O. The alloy of copper and zinc is brass, the alloy of copper and nickel is cupronickel, and the alloy of copper and other metals is bronze.
Brass
Brass is mainly an alloy composed of copper and zinc, which is characterized by high wear resistance, high strength, high hardness, chemical corrosion resistance, and good cutting technology. Seasonal cracking (stress corrosion cracking) often occurs in brass, which is obvious in ammonia, ammonia or sulfuric acid. There are three reasons for quaternary cracks in brass, one is pitting corrosion (electrochemical corrosion), the other is dezincification, and the third is residual stress.
The brass classification is as follows:
- Add Zn, which is only composed of copper and zinc, called ordinary brass, used to make copper plates , copper tubes, etc.
- Pb is added, in addition to copper and zinc, there is also lead. The cutting performance is particularly good. It is called quick-cut brass, which has good castability and good fluidity.
- Sn is added, in addition to copper and zinc, there is also tin, which is corrosion resistant and used in marine climates.
- Add AI to improve strength, hardness, and corrosion resistance in the atmosphere, which is used to manufacture corrosion-resistant parts.
- Add si to improve mechanical properties, corrosion resistance and wear resistance, and used to manufacture sea-going ship parts and chemical machinery parts.
- Add Mn, such as 58-4 (L105), often used as brazing filler metal, with good high temperature wettability.
- Adding Ni has good heat and corrosion resistance.
- Fe is added, with good heat and corrosion resistance.
Cupronickel
Cupronickel refers to a copper-nickel alloy, which is silvery white. Pure copper and nickel can significantly improve strength, corrosion resistance and hardness, and reduce the temperature coefficient of resistivity. Compared with other copper alloys, cupronickel has better mechanical and physical properties, especially heat and corrosion resistance.
Cupronickel is classified as follows:
- Add Ni, simple nickel-nickel-nickel alloy.
- Adding Zn, in addition to nickel, also contains zinc called zinc cupronickel, which has good workability and corrosion resistance.
- Adding Mn, nickel is too expensive, replacing nickel with manganese is called manganese cupronickel, which has a wide temperature range.
- Adding Fe, in addition to nickel, it also contains iron called cupronickel, which has low cost, high strength and good corrosion resistance, especially good corrosion resistance against flowing seawater.
- Adding AI, in addition to nickel, it also contains aluminum called aluminum cupronickel, which is corrosion-resistant, and is used in the manufacture of various high-strength corrosion parts in shipbuilding, power, chemical and other industrial sectors.
Bronze
Bronze is a collective term for all copper alloys except copper-zinc and copper-nickel alloys. It has the advantages of low melting point, high hardness and strong plasticity, and is suitable for casting various appliances. Its classification is as follows: tin bronze, aluminum bronze, beryllium bronze, silicon bronze, titanium bronze, zirconium bronze, cadmium bronze, manganese bronze and chromium bronze.
Aluminum and its alloys
The main characteristics of aluminum
- Aluminum is a silver-white light metal with a density of about 2.72 g/cm3, which is about 1/3 of pure copper.
- The heat capacity and latent heat of aluminum are high. The melting point of pure aluminum is about 661 ℃. The boiling point is about 2450 ℃. Its oxide Al2O3 has a melting point of about 2 050 ℃.
- Aluminum has a face-centered cubic structure.
- Industrial pure aluminum has a high plastic plate (Z=80%) and can easily withstand various forming processes, but its strength is too low. Therefore, pure aluminum can only be used as a structural material after its strength is improved by cold deformation strengthening or alloying. .
- The linear expansion coefficient of aluminum is 23.5x10*/9 (below 100 C), and its elastic modulus is 70 GPa.
- The electrical conductivity of aluminum is about 60% of copper, the resistivity is 50% of copper, and the thermal conductivity is 70% of copper. The order of conductivity of common metals from high to low is: Ag, Cu, Au, Al. In short, aluminum has low density, good plasticity, easy processing, good corrosion resistance, and abundant resources. The content of aluminum in the crust accounts for about 7.73% (mass fraction).
Classification of aluminum alloy
Aluminum alloys can be divided into cast aluminum alloys, deformed aluminum alloys, non-heat-treated strengthened aluminum alloys and heat-treated strengthened aluminum alloys. Elements often added to aluminum alloys include Si, Cu, Mg, Zn, etc.
The characteristics of cast aluminum alloy: low strength, low cost, large fluctuations in the chemical composition of the material, poor mechanical properties, but good fluidity.
Features of wrought aluminum alloy: high strength, strict composition requirements, and good mechanical properties. Aluminum alloys that cannot be heat-treated and strengthened include AI-Si series and AI-Mn series, and aluminum alloys that can be heat-treated and strengthened include AI-Cu series, AI-Mg series and Al-Zn series.